ADCA Transforms Quality Monitoring with a Dedicated IoT Platform - DEEP
ADCA Transforms its Quality Monitoring with a Dedicated IoT Platform
Discover how ADCA revolutionized the quality monitoring of its cathodic protections: a tailor-made IoT platform capable of centralizing over five million data points per year, offering instant visibility, both on-site and remotely.
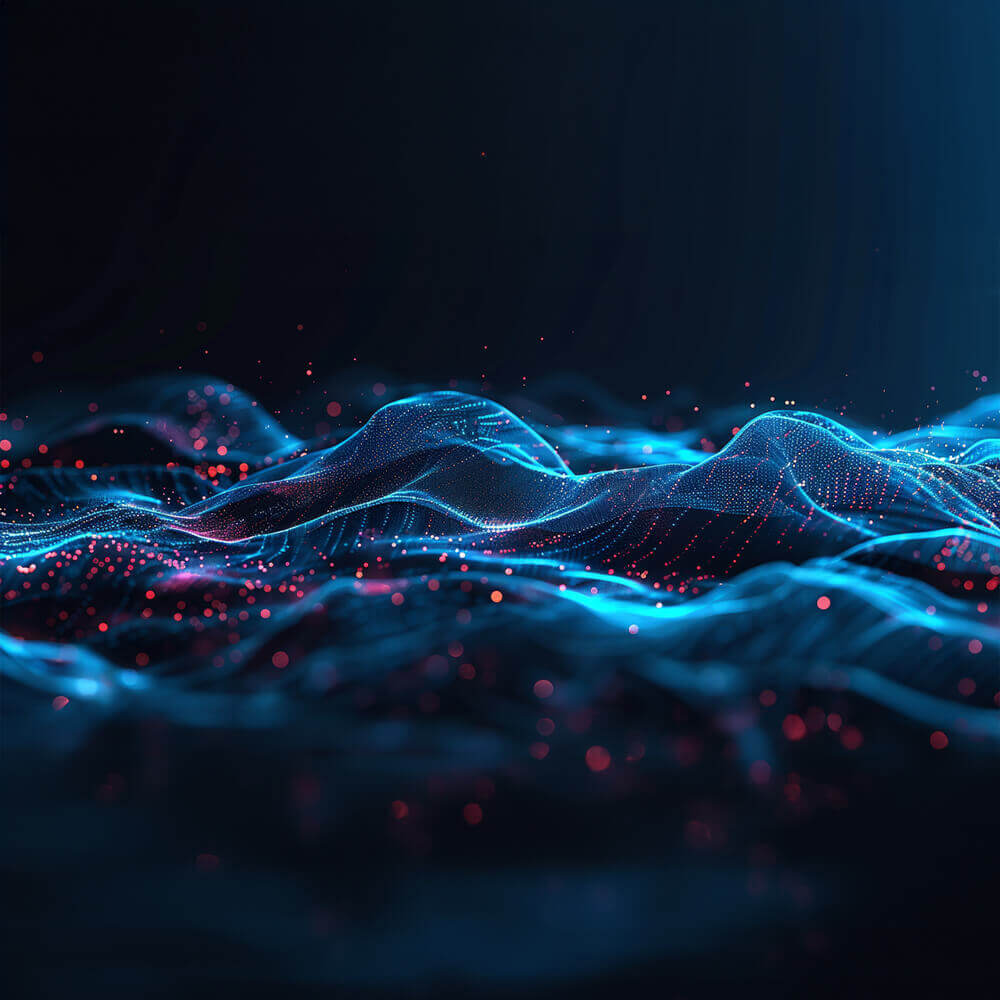

Context & Challenges
ADCA already had an initial IoT platform, but it was reaching its limits: inflexible, difficult to deploy at end-customer sites, and unable to easily display large volumes of data. Their ambition was therefore to transition to a more technical and professional solution, capable of growing with their needs.
Client's Activity:
ADCA designs, produces, and markets cathodic protection systems aimed at preventing corrosion in buried pipelines. Their activity leads them to instrument clients' equipment with IoT sensors for real-time quality monitoring.
Support Model:
DEEP provided end-to-end support: functional and technical framing, development of a containerized platform, cloud or on-premise deployment, and then operational maintenance (MCO) for end-users.
Damien CAPAÏ - General Manager at ADCA
Mission Objectives:
- Centralize and ensure data reliability: Aggregate all field sensor readings into a single point to facilitate analysis.
- Real-time visualization: Enable teams and clients to easily view curves and key indicators.
- Scalability & portability: Make the platform quickly deployable in the cloud or on client infrastructures using Docker containers.
- Predictive maintenance: Generate automatic alerts to anticipate breakdowns and quality deviations.

The Support Process
Business workshops were conducted to define quality indicators, target data volume, and data export requirements.
This involved creating a micro-services architecture, implementing a progressive loading algorithm to display over 5 million data points, and using Docker packaging to ensure consistent deployments.
The platform was installed at ADCA and then at the first end-clients, with 24/7 supervision and continuous evolutions provided via Digora's managed service.
Client Benefits
- Controlled Quality: Instant visibility into the performance of cathodic protections.
- Reduced Unplanned Downtime: Automated alerts allow intervention before a breakdown impacts production.
- Time Savings for Technicians: Remote consultation and diagnosis, reducing on-site travel.
- Sustainable and Evolving Platform: Containerized architecture ready to integrate new features proposed by end-users.
